Six things a good WMS picking module must do
An argument can be made that there is only one thing a good WMS picking module must do, and that is to allow you to fill as many orders as you can as efficiently as possible. While this philosophy is rooted in a good deal of common sense, the key word is ‘rooted’. If businesses need the ability to adapt to survive, there are six features a good WMS picking module contains that you should ask about in the sales cycle.
1. Multiple picking strategies
The most robust feature that WMS systems bring to picking is multiple picking strategies. Chances are good there are a lot more strategies on how to arrange a pick list than you think: wave picking, batch picking, bin picking, pallet picking, and two stage picking are just a few.
Find WMS with a suitable picking module using our completely up-to-date WMS vendor directory
Consider: what is the criteria for prioritizing? Can one picker work on multiple orders at a time? Can multiple pickers work on one order? Is lot tracking, or shelf life management an important component in your picking strategy? It is not unusual for pickers to spend as much as 60% of their time traveling between pick locations. Are you sure your pick strategy is the best for achieving your business objectives? More importantly, is it possible you might need different, or multiple strategies in the future?
2. Cross docking/direct-to-truck loading
Some may say these are just a specialized picking strategy, or conversely, that both represent the absence of picking. These merit mention on this list because they represent a different way of making money that traditional receipt/put away/pick load models. Even if you do not cross dock or direct load currently, you want a WMS picking module which supports these activities.
3. Wireless functionality
Good WMS picking modules can be directed wirelessly. Whether you have an immediate need or not, it is inevitable that the future will contain more wireless applications than today. Wireless technology is a simple investment in where the technology will be growing.
4. Lack of constraints
Are there any constraints on picking units? Does your WMS picking module work equally well for pieces, cases, drums, and pallets? Does the picking module support full pallet picking?
5. Documents and labels support
Can the module support any required labels and documents in the required format? Again, this is potentially a crossover requirement with packing and loading, but as designs become more efficient, the lines between these functions are likely to become more blurred.
6. A well-designed UX
Does the picking module contain features which will make it easy to learn for your workforce? Assume that you will be teaching a new picker how to use this technology every week. Would it be a 30-minute task, an all-day task, or a never-ending task? Do the screens promote self-learning? Are there clear help messages when errors occur? Are error messages clear, or do they refer to obscure codes?
The traditional goal of picking is to make it as productive as possible at the lowest cost possible. In order to use technology to making picking more effective, it is essential to choose a solution that can change and adapt as the business evolves.
Free white paper

WMS vendor directory
Save hours of WMS vendor research with this free guide
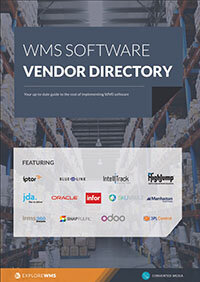
Featured white papers
-
-
-
WMS requirements template
Over 120 WMS feature ideas to help you build a requirements list and shortlist vendors
Download
Related articles
-
How much WMS software costs and how to set your budget
A complete guide to WMS costs, and how to calculate your budget based on these
-
Mission-critical features of food lot traceability software
What features of food traceability software will help you during a food recall
-
Warehouse picking and packing processes: how much labor do you need?
Logiwa's Erhan Musaoglu shows you how to calculate picking and packing labor requirements for you...