Mission-critical features of food lot traceability software
A food recall is a serious issue for any food business. That’s why finding software to support your company throughout difficult procedural processes is so important. Your system should be able to handle every aspect of your food manufacturing process from the delivery of the ingredients all the way through to the manufacture of that product and its journey to a supplier.
Let’s look at an example scenario, and how each feature of a food lot traceability software can aid that process.
This morning has been pleasantly quiet and you are getting a lot of work accomplished. Then, the phone rings, and one of your grocery customers says there is a potential problem with a jar of pasta sauce.
Feature #1: full ingredient traceability
Now you’re aware of a potential problem, you get the lot number from the jar and start to work collecting data. You learn when the lot was produced and packaged. You find the lot identifiers of the mushrooms, vegetables, and tomatoes used to make this sauce using your system. Data on the equipment used for cooking is ready. All you need to know about the jars and lids are ready.
Feature #2: complete product tracking
Your WMS provides even more for you. Your product tracking system shows that you received 5,500 gallons of diced tomatoes on the tenth of the month. You know where those tomatoes were processed, who was the carrier that brought them, and the exact number of the tank trailer that delivered those diced tomatoes.
Your crew pumped the tomatoes into portable vats kept in your warehouse. You have the cleaning records for the vats and you know the temperature of the warehouse room through the entire time those tomatoes were on hand. On the day the pasta sauce was prepared, your forklift moved a vat to your production staging area. Standard quality checks showed the diced tomatoes were up to standards and ready for processing.
Feature #3: extended lot visibility
Your system allows you even more flexibility to look further back in time and tells you the farm where the tomatoes were grown and specifically in which field. You also know the date of the harvest and all the transportation steps toward the supplier where those tomatoes were diced.
That lot of diced tomatoes was also used to produce another product. You can see the precise lot numbers for the finished product and where they now are. Some have been shipped to grocery stores and other products in those lots are still in your inventory. About half of the diced tomatoes are in your warehouse at this time and none are required for production scheduled within the next few days.
Feature #4: robust recall process
Less than an hour after receiving that phone call from your grocery customer you have completed an initial incident report and you are ready to recall products from your customers and quarantine any inventory on hand whether that is made up of diced tomatoes or finished products that have not yet shipped. You can alert any of your customers quickly if that is needed. You can alert the supplier that diced the tomatoes for you and the farmer who grew the tomatoes.
All the information you gathered in mere minutes using your food-specific software can be used to immediately identify and isolate production, as well as start any major food recalls. You’ve saved precious time at one of the most crucial moments in your business.
Feature #5: certification management
You can ensure complete compliance with all your customer requirements. You are ready to show compliance with all the FDA already.
How is it possible to collect so much critical data in so little time? Your WMS and ERP are designed for a food processing business like yours. You have set up those systems specifically for your business and you know all the people in your business follow established procedures to safely handle their jobs and record the steps and operations they use without fail.
Feature #6: smart device enabled
The FDA has performed audits. Your customers have audited your processes to ensure you can deliver products that meet their requirements and satisfy every requirement of your industry. You regularly perform internal audits and you have a well-defined training and certification program for all the employees involved in any aspect of your food processing business. Your warehouse environment is monitored constantly and all the critical conditions are recorded automatically.
We still do not know if there is a problem with that jar of pasta sauce. More testing is needed. No matter what the results of those tests show, you are ready to quickly perform all the required notifications right now because you have the right WMS with the right features and you know how to use it.
Free white paper

WMS selection checklist
Over 100 actionable steps to WMS selection success
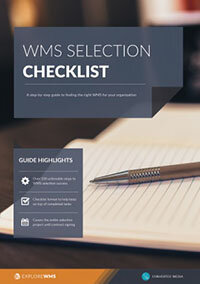
Featured white papers
-
WMS requirements template
Over 120 WMS feature ideas to help you build a requirements list and shortlist vendors
Download
Related articles
-
Your complete WMS features and requirements guide
How to gather requirements for a new WMS, and features to look for to meet them
-
Mission-critical features of food lot traceability software
What features of food traceability software will help you during a food recall
-
Here's your complete WMS modules and features checklist
All the features and modules you might need in your WMS - perfect for requirements gathering