Your complete WMS features and requirements guide
You're ready to select your WMS system. You want to make your warehouse more efficient, reliable, and profitable - but what does this mean in a system?
The WMS features you pick and prioritize will have real-world impacts on the day-to-day running of your warehouse. Prioritize the wrong functions, and your warehouse won't realize the benefits of your system - and it may even make existing processes worse.
We've created this guide to WMS features so you can move through the jargon and find the actual tasks you want your software to perform. We'll sort through your WMS requirements so you can prioritize the modules that your warehouse needs, and walk you through how to present your needs to potential WMS vendors.
Our WMS features and requirements guide covers:
- What WMS features are considered standard
- What advanced WMS features are also available
- How to create your prep list to understand what you need and what you should ask for in your WMS
- When you might want to consider bringing a customization request to your list of potential WMS vendors
So, let’s begin by looking at how to select the WMS features that work best for your business.
1. Map out problems you want a new WMS to solve
Understanding the need for a warehouse management system starts with asking questions about your business, especially if you’re concerned that your operations aren’t as productive or profitable as you think they could be.
Look at every activity that your warehouse plays a role in, from order fulfillment and shipping to inventory costs, labor costs, equipment challenges, and needs that aren’t being met. Here are a few common questions you can ask yourself to start creating a list of problems you want to address:
- Are inaccurate orders or inventory levels negatively impacting your business?
- How long would it take you to verify inventory levels or overall order accuracy?
- What do you need to create, pack, and ship orders accurately? Do you have any of this already?
- How many manual processes are involved from receiving an order through fulfilling it and recording it as complete?
- What are the biggest complaints in your warehouse today?
- Who works in your warehouse? What do they do? How do they share their work status?
- What information does your warehouse leadership need to make a strategic change? Do they have access to this?
Those concerns will help you set out a scope for your WMS and make sure that the features and requirements you present to vendors are right for your business. Before you get too far involved with specific companies or vendors, however, there are a few things you’ll want to get together internally.
We’ve put these internal items in the checklist below to help make your WMS selection process easier and to get you to the right, realistic mindset for exploring WMS functionality. They’ll keep you grounded even as you see shiny new software that promises to solve all your problems but could break the bank.
Your quick prep checklist for WMS requirements gathering
Internal elements you must secure | |
---|---|
Senior management support | Get an executive sponsor for your efforts even as you start to review requirements and options. It will give you credibility when asking for the financing and minimizes the chance that the project is pulled during its later, costly stages. |
Clarify the need for your change | You might “know” that your warehouse needs a management tool, but can you articulate why? Can you explain savings you expect and the benefits your company will see? Is there a customer you can better serve and gain a positive ROI? |
Outline a budget | Different functionality, which we’ll review in a moment, comes with different costs. Work with leadership to know how much you can spend on the system based on today’s cash-on-hand as well as the savings or other ROI you expect a WMS to generate. |
External items to seek out | |
Key stakeholder input | What do key user groups want from a new WMS? You won't know unless you ask them, and selecting a system that doesn't meet their needs will result in lost productivity and poor user uptake. Survey everyone who will be impacted by the change for the most accurate requirements list possible |
Recommendations from others | Ask your contacts and contemporaries which platforms they like or use. If you have a successful competitor, look to see which system they use — you can search the internet for case studies to see if your rival is mentioned. |
Experience on your team | Look for any expertise or experience that you already have on staff to see what works and what doesn’t. Get creative, such as turning to HR for new talent to see who might be worth your time. |
Start reading and watching | A WMS is never a trivial investment. You’re going to be spending some considerable time and money on any adoption. So, it’s time for homework. Read materials that WMS vendors provide and look at review and comparison services to understand what’s available and who is well recommended. You never want to be surprised (or let down) once your selection process is done. |
2. Learn about core WMS features and what they do
Building out your warehouse management system features list starts with knowing what is possible and thinking about what your warehouse needs right now, plus what you might want in the future. We suggest you put together a WMS features checklist that addresses both current and potential needs because it may help you with the selection process when you reach that stage.
Let’s take a moment to review some of the more essential functions of warehouse management and how it can help you achieve common warehousing goals such as improved inventory accuracy, reduced inventory quantities, and better pick-and-pack in your day-to-day operations.
Use this feature set to start building a WMS requirements template when you put together your RFP:
Picking
- Your most desired function, picking functions are used to guide workers to follow to fill the orders you have received.
- Basic functions should include support for mobile scanners and other handhelds as well as the ability to generate complete lists and packing slips as orders are created.
- Look for a system that is designed to adapt to warehouse spaces or is built for one like your existing layout.
Receiving
- Covers the receipt of goods from your partners and customers. This feature set should include the ability to receive and add both scheduled and unscheduled deliveries to your warehouse and inventory counts.
- Most WMS will also include some returns management, quality assurance tools, and the ability to re-number or breakdown goods that are received in one quantity but shipped in another.
Storage and inventory management
- Processing of delivered goods and the ability to allocate warehouse space to them. This may be automatic or manual space allocation.
- Typically includes the ability to process goods and store them in single-load or mixed-load options.
Counting
- Accurately track all of your inventory across every stage and warehouse location with the WMS’ counting feature.
- Counting systems should link up to your picking and receiving activities to maintain an accurate count and provide real-time data on your inventory.
- Most WMS will offer cycle counting: a method that counts a few products each business day throughout the year to verify that inventory levels are accurate.
Warehouse control and management
- Warehouse control tools allow you to run your operations with an “on the fly” approach that responds to needs and orders as they happen. This may be one of the most significant shifts from a core feature if you’re currently using a manual process.
- Cross-docking is one of the most common warehouse management tools in a WMS, and it will allow you to route goods you are currently receiving to fulfilling existing orders, using them before they are stored on your dedicated shelves.
- Another core feature to look for is the ability to track goods as you relocate stock in your warehouse. This process should be simple for both individual items as well as lots because you may need to change stock orders and location as your business changes.
Tracking: lot and serial
- Lot and serial number tracking allow you to maintain a stricter control of your inventory to ease order fulfillment and re-orders of your stock.
- With tools like bin-level tracking and count validation as you pick, you’re able to optimize order fulfillment and receive an automated audit tool.
- This can be an essential requirement for businesses whose customers provide restrictions on fulfillment, such as requiring that shipments do not contain mixed lots.
Order allocation
- Order allocation is a top warehouse management system functional requirement because it allows you to make the most of your inventory to meet current orders.
- This module allows you to input orders from a variety of sources and dynamically create an order list to fill, assigns picking tasks to employees, and prioritizes based on characteristic you define, such as filling back-orders first.
Group or wave planning
- On a good day, you’ve got almost too many orders to fill. Wave planning tools allow you to create your own picking strategies to meet current demand and adjust when orders or priorities change. Look for support for multiple picking strategies.
- Many systems now come with sorting options as well as customizable configurations to support picking by bin locations, pallet quantities, based on shipping cartons for serialization, and more.
- Today’s wave picking features focus on supporting your operations beyond the initial functionality of allowing pickers to gather goods for multiple orders simultaneously.
In this list of WMS system features, you will find a variety of tools and capabilities that support almost any type of business. If you’re considering a functionality checklist for a pure B2B operation or for one that blends B2B and B2C sales, it’s the additional layers and supports that make the difference.
Use this WMS requirements template to find, shortlist and prioritize features for a new WMS
For example, order allocation modules that also support B2C operations will need robust integration capabilities, so you can tie your e-commerce website and ERP system to the WMS, ensuring orders flow smoothly. Why? Because 44% of U.S shoppers use online and in-store purchase and pickup options simultaneously.
While this has been a deciding factor for many in the past, the current trend in most industries has been to replicate B2C interfaces in B2B spaces. As more companies provide online sales portals for their B2B efforts, we expect to see fewer differences among lists of among B2B and B2C WMS feature sets.
3. Research advanced and specialty WMS features you might need
When looking beyond core functionality, there’s one question that should guide your creation of a warehouse management checklist: What sets my warehouse and my business apart from others?
Look at your business processes and needs that help you run efficiently or provide a better service than your competitors. Take that knowledge and seek out modules and WMS system features that match.
Here are just a few special and advanced features currently on the market that may help you shape your WMS features checklist:
- Specialty materials support: properly track and trace specialty materials that have a unique business or regulatory compliance requirements, such as hazardous materials or goods that cannot be left unattended.
- Advanced verification tools: robust modules that support multiple devices and multiple layers of order tracking and verification, following your goods and orders across lot number, serial number, trailer label, and more.
- Pre-staging tools: if you offer multiple DCs or retail locations, you may want a WMS that contains tools designed specifically to help you pre-stage goods and help you optimize orders through warehouses based on multiple factors of need, location, and inventory levels.
- Exception management: a smart WMS can save you money. If your setup is complicated or you have special shipping cases based on weight or size, you might consider an exception management module. These will help flag difficult orders and move them out of processing lanes, so you can address their unique needs faster and not create bottlenecks in picking or packing.
- High-volume returns support: for B2C brands and B2B companies with a large e-commerce focus, you’re going to experience returns, and they may spike due to unforeseen circumstances. Your WMS should be able to scale to make returns as painless as possible.
- Robust food-recall tools: for food businesses, strict government regulations for food recall procedures are in place, so your software should support the recall process to make it as simple as possible.
Need help creating your warehouse management system advanced features list? Look at these articles for a hand:
- Five features a good e-commerce WMS needs
- Four key features to look for in a manufacturing WMS
- Key features wholesalers should look for in a WMS
- Six advanced WMS features to consider during requirements analysis
- Six features to look for in a retail WMS
- Six key features to look for in a 3PL WMS
Special consideration: WMS analytics
Analytics and benchmarking tools are becoming more common WMS features because of the readily available nature of data and processing engines. It’s getting easier to understand business thanks to systems that generate and share their data more freely.
Beyond some initial data and analytical capabilities that are moving into the realm of standard offerings — such as average time to fill orders and total landed costs of orders or items — you may want to look for additional analytics packages that can support your business.
Top choices include inventory optimization tools that can help you plan your warehouse layout and picking routes based on goods you ship most often; replenishment analysis specific to customers or target regions; workforce management tools that track individual user’s accuracy and speed; and synchromodality tools.
The business intelligence market is expected to reach $18.3 billion by the end of this year, according to Gartner. Analytics is the engine that powers that market, so having and using internal data will soon become a business requirement instead of an advantage. It’s one of the more important advanced features to look for in a WMS because the ability to grow your analytics usage will play a role in overall company viability.
For more on analytics capabilities to consider adding to your WMS functionality checklist, see five analytics features to make the most of your WMS data.
4. Consider making requests for WMS specialty features
Nearly 80% of companies with “high-performing supply chains” report higher levels of revenue growth than the average company in their industry. Achieving that level of performance often comes down to optimizing processes and software to run more efficiently and quickly respond to business changes or problems.
Ask yourself: what do you need to take your warehouse to that next level?
In some cases, it’ll be a core feature: 46% of SMBs either don’t track or manually track inventory levels, so standard inventory automation can help you excel.
In others, advanced features can help you reduce costs: U.S. retailers have roughly $1.43 in inventory they have to stock and track for every $1 in sales they produce.
But, in your case, it might be a feature we haven’t touched on yet. Perhaps it’s a business need to integrate with legacy or custom software that your business demands. Or, you see demand spikes around specific events like natural disasters and want to forecast inventory levels based on multiple data sets. Perhaps you need a user-interface that supports voice commands for everything, or you’ve got such a noisy floor that you require every command to be displayed visually on Internet-connected goggles.
Find WMS vendors offering the features you need with this comprehensive WMS vendor directory
Warehouse management system functional requirements are whatever you need to run your business better. If you’ve got a need that isn’t standard, reach out to vendors to see what support is possible.
There’s a healthy tradition of customization in warehouse management functionality and features lists. Many of today’s leading WMS were initially built to serve a single customer and then slowly developed and enhanced with new features and requirements as those companies gained new customers. So, you might have something that vendors have seen before.
That about does it for our guide to WMS features and requirements templates. Let’s end with one more thought: Your business deserves a WMS that works for you. If something doesn’t meet your needs, the market is large enough that you can keep looking and will likely find something that does.
Free white paper

WMS requirements template
Over 120 WMS feature ideas to help you build a requirements list and shortlist vendors
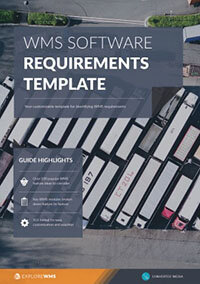
Featured white papers
-
WMS requirements template
Over 120 WMS feature ideas to help you build a requirements list and shortlist vendors
Download
Related articles
-
How much WMS software costs and how to set your budget
A complete guide to WMS costs, and how to calculate your budget based on these
-
Mission-critical features of food lot traceability software
What features of food traceability software will help you during a food recall
-
WMS implementation guide including checklist & project plan
A guide to the entire WMS implementation process - from change management planning to go-live