WMS inventory modules: going beyond the basics
‘How will WMS software help me achieve better inventory control?” This is a fair question, since the process for inventory management – how to account for receipts, shipments, and to verify accounting occasionally with physical counts - was first defined in ancient Egyptian hieroglyphics, and hasn’t changed much since. Technology certainly isn’t a prerequisite for inventory accuracy; banks have recognized the need for 100% inventory accuracy (cash) since the middle ages.
However, the world today is complex. If you handle all of your warehouse business within four walls; if you do only domestic business; if your stock comes in, goes out, and you get a small fee for handling each transaction, inventory modules which go beyond the basics might hold no value for you.
However, if you are a participant in the global economy with its conflicts, competition, requirements, and changes, you may want to consider some of the following advanced inventory functionalities:
Multiple locations
What happens when your business has grown enough that you need to expand into another location? How will that location be configured in your WMS inventory module? What if you subcontract with someone to manage your inventory for you? Will you have inventory control there? Inventory visibility?
Find the right WMS inventory module for you using our comprehensive WMS comparison engine
What if you have inventory in transit on ocean containers? Who owns that inventory? When is that inventory available for sale? Is that inventory included in replenishment calculations?
Will you engage in any toll manufacturing, or commission processing outside of your warehouse, but still under your financial ownership? What are your inventory controls at those locations? Will your WMS inventory module offer inventory visibility?
Multiple currency
Will you have warehouse operations in foreign countries? If so, will your WMS software facilitate inventory valuation in multiple currencies?
EDI transactions
Do your customers or suppliers require support for EDI transactions? The B2B trend seems to be leaning toward more flexible web based transactional tools, but if EDI is a requirement, it is a complicated one.
Costing
How does your inventory costing system work? How are fixed costs allocated to your products? Are you in compliance with IRS regulations regarding inventory valuations? Are you minimizing your tax liability with your inventory accounting and costing process?
Product traceability
Does your inventory need traceability? Are there characteristics beyond SKU and quantity that must be attached to the inventory record? Does your inventory need a unique handling or serial number?
Barcode/RFID support
Does your operation utilize barcoding, or wireless RFI devices? What about RFID chips? Tablets on forklifts? Will your inventory system support those technologies?
Consignment
Do you engage in any consignment inventories? How is the book value calculated and reconciled?
If you think about your operations, you can probably quickly add your own special situations to this list which will either require some inventory sophistication, or business process change. Sometimes, it is easier and more profitable to change the business model. But in most cases, you do things for a reason, and those reasons may require an inventory module which goes beyond the basics.
Free white paper

WMS vendor directory
Save hours of WMS vendor research with this free guide
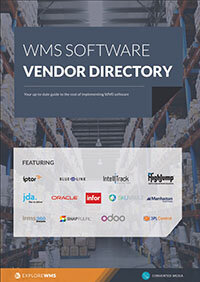
Featured white papers
-
WMS requirements template
Over 120 WMS feature ideas to help you build a requirements list and shortlist vendors
Download
Related articles
-
Your complete WMS features and requirements guide
How to gather requirements for a new WMS, and features to look for to meet them
-
Mission-critical features of food lot traceability software
What features of food traceability software will help you during a food recall
-
Here's your complete WMS modules and features checklist
All the features and modules you might need in your WMS - perfect for requirements gathering