The evolving warehouse and future trends
To date, a large proportion of warehousing activities and processes are still being performed manually, resulting in shipping delays, wrong products being picked and additional costs that are eating about at company bottom lines. However, with new technologies such as cloud software, augmented and virtual reality, drones, robots, autonomous vehicles, IoT, and wearable devices will without a doubt transform the world of warehousing over the coming years. With the support of artificial intelligence, big data, and advanced predictive analytics, warehouse planning and analysis is expected to evolve to the next level.
How can existing or future warehousing infrastructures leverage these new trends?
Drones and Robots
Today's inventory management requires workers to scan items manually, which is a time-consuming error-prone process. It's impossible to keep track of all items in the warehouse manually. Can drones and robots be the future?
The industry is buzzing with the talk of drone and robots use within warehouses. It wasn’t that long ago, drones and robots carrying out the work of warehouse staff seemed a far-fetched idea. However, in larger warehouses, flying drones and robots now patrol distribution warehouses regularly and are fast becoming the norm. They've become workhorses of the e-commerce era online that large retailers such as Amazon can't do without.
Two drones can do the work of 100 humans over the same time period, according to supply chain specialists. This means they can do several tours of a warehouse - even at night - compare results, identify discrepancies, and build up a much more accurate picture much more quickly.
Unmanned aerial vehicles (UAVs) – drones, can be successfully deployed to upgrade warehousing processes. A good example is the special aerial drones using optical sensors (cameras) which can help locate an item in a warehouse or scan the respective RFID tags at a distance of tens of meters. In larger warehouses, a drone system can be used to gauge inventory levels and transmit the data directly to the warehouse management system. This will facilitate the fast detection of individual items and prevent inventory mismatches.
Drone makers claim scanning accuracy of close to 100%. It is driving down warehouse costs, but it is also putting people out of work? Are they safe?
Despite drones appearing to be a winning technology, outperforming other technological applications in speed and accuracy and many companies eager to jump on the latest tech bandwagon, it’s important to look at the limitations prior to rushing in. Drones must overcome a number of limitations, such as safety, payload capacity restrictions, and political acceptance before they will reach a high level of adoption.
Packaging goods
Robots are also evolving in the tail end of the warehouse process. Packing often involves customization and last-minute requests from customers to modify or co-pack items. This is a time consuming and labor intensive activity that requires flexibility. Co-packing usually means opening a box, taking the items out, potentially applying a sticker, and repacking the items. A collaborative robot, designed to work safely around humans, can support and improve this manual process. Warehousing robots can handle objects with their hand-like extensions and are able to perform almost any task a human can do. The warehouse worker can quickly teach the robot a task which it can then perform over and over again. Their ability to learn new tasks on the spot allows for the necessary flexibility.
The Changing Face of Devices in the Warehouse
Smartphones and tablets have made their way into the business landscape. Sales personnel are using iPhones out in the field to close sales and update customer information. Retail stores use mobile phones equipped with credit card scanning devices to speed up the checkout process during busy seasons. Business executives use tablets to stay connected to business activities even while they are away from the office, and customers order products and services through their mobile devices every day.
One of the key ways that warehouse has been changing and will continue to evolve, is the use of handheld devices for warehouse management. A recent study showed that by the end of 2018, only 12% of respondents expect to still be using pen and paper-based processes; 66% plan to use handheld mobile devices with real-time access to WMS systems.
In the past, only large expensive rugged devices were seemed fit for purpose. However, it has become all-too-natural to ask how smartphones, Android devices, wearables etc could be used as a cheaper, more familiar alternative to bulky and expensive RFID guns that were a fixture in most warehouses.
Mobile devices are becoming more “gun-like”
Years ago, using a smartphone to scan barcodes was a near impossible task, as the average camera on a phone was not designed specifically for that purpose. In recent years, technology has evolved considerably and hardware suppliers are adopting smaller mobile devices to warehouse tasks and environment:
Holders allow smartphones and tablets to take on different form factors, including one approximating the typical RFID gun, increasing comfort and usability.
There are a number of mobile-device-compatible scanners, overcoming the limitations of the average smartphone camera.
Mobile devices are now more durable, and additional cases, holders, and films make them even more suitable for rough warehouse environments.
Many holders and add-on devices come with additional batteries for extended battery life.
This means that mobile devices are becoming more “gun like,” erasing the major differences between them and traditional RFID guns. With changing in software technology such as the cloud, IoT, trends of BYOD and tighter security on data enables warehouses to have an array of devices. In response though, hardware manufacturers are creating RFID guns devices that are less expensive and less bulky to try and compete with the mobile solutions market. The introduction of Android affordable rugged mobile devices has truly set the competition between consumer versus rugged devices alight.
The shift in warehouse trends has become even more pronounced with the cloud.
Cloud software allows updates to be made on an ongoing basis, meaning minimal disruption of normal operations and a guarantee of up-to-date software. Instead of deploying software solutions on local servers (which need to be maintained), software is hosted off-site, usually by the software’s creators. Many companies these days are selecting Cloud Supply Chain Management Solutions to gain better control over their inventory in an increasingly complex distribution environment. In fact, a recent WMS report found that 91.5% of businesses were considering a cloud-based WMS in their current selection project. Cloud technology is a powerful, cost-effective tool that is readily available to help you face your distribution challenges head-on and stay one step ahead of your competitors.
In the next three years, Warehouse Management System (WMS) Technology has been available in the cloud delivery model from some providers for a few years now, offering a lower cost, reduced risk option. When evaluating WMS providers, it is imperative for every business to understand the total cost of ownership (TCO)—including both direct and indirect costs—of the technology and labor associated with adopting WMS technology.
Cloud technology allows smaller businesses to act faster than big, established competitors. Pay-as-you-go service and cloud business applications mean small outfits can run with the big boys and disrupt the market while remaining lean and nimble.
As mentioned above, cloud computing software provides businesses with greater flexibility, reduced risk and lower total cost of ownership. Small and Medium-sized companies are now able to utilize higher quality software which 5-10 years ago was not cost effective for them to use. This means those businesses are better equipped to deal with the day to day challenges of doing business in 2018. Make sure your company is taking advantage of this revolution and do not get sucked into buying legacy software that will hold you back.
While some see the cloud as being simply the next level of technology, the shift towards cloud computing also has very tangible benefits. See key benefits
Given the forever changing business and technology landscapes, warehouse management is growing increasingly complex and critical. Now with the help of Internet of Things (IoT), 3PLs can optimize the utilization of their warehouse space in a more robust and effective manner.
Big Data, IoT are changing the face of warehouses and creating smarter warehouses
Consumer expectations continue to grow and are expected to drive continued investment in IT and operational functions in warehouses over the coming years. Increased connectivity is everywhere, as tech companies make everything from heating systems to refrigerators internet-ready.
Leveraging the latest supply chain technology and the Internet of Things (IoT), a “smart warehouse” can now serve as a hub to boost efficiency and speed throughout the entire supply chain. From wearables on workers to sensors and smart equipment, internet-enabled devices and technology can profoundly change logistics management.
Connected devices and sensors can help manage the right quantity of products, at the right price, time and place. The objective is to manage the route (journey) of merchandise from the pick-up point to endpoint, including pickups, reception, quality control, reporting, and forecasting etc. Across Warehouse Management Systems, there is a need to allocate every square meter effectively to ensure easy retrieval of specific goods followed by processing, and speedy delivery. Integration of IoT with Warehouse Management System (WMS) leads to the true development of pull-based supply chains (rather than push-based).
3 Ways Supply Chains will benefit from the IoT
- A Smarter Warehouse: Embracing the IoT grants supply chains the ability to operate a hyper-efficient, optimal warehouse. The result (and subsequent impact on the bottom line) is a reduction in asset losses, temperature stability, and total warehouse inventory optimization and accuracy.
- A Responsive, Continually Improving Supply Chain: In an omnichannel marketplace, organizations that ramp up utilization of the IoT will enjoy a highly intelligent, transparent and responsive supply chain that continually improves itself. The IoT platform will allow supply chains to accurately locate, track and measure the movement of inventory through sensor technology and will have the agility needed to speed up or slow down based on the dictation of customer demand.
- A Deeply Intelligent Supply Chain: With enhanced connectivity, supply chains will feel the impact of intelligence on every area of their business, including financial, customer support, marketing, sales, and operations. By boosting forecasting accuracy and demand planning capabilities, organizations will be able to focus on the right tasks at the right times, leading to significant cost and time savings.
A warehouse may still use printed pick lists or may have adopted pick by voice or other technological aids. But a warehouse using the Internet of Things devices can direct a picker to the right spot in the warehouse faster and with more information. An IoT-equipped warehouse may upgrade to automated guided vehicles to retrieve items. Sensors in the warehouse can detect locations of people, vehicles, and merchandise and can transmit locations and events to warehouse managers and management systems. Additionally, employees using smartphones or tablets can load boxes or pallets on a truck in the correct order for shipping.
Save hours of WMS vendor research with our free independent vendor director
Improved predictability and planning
Conventional warehouse planning and analyses can be enhanced through big data, artificial intelligence, and advanced predictive analytics. With the help of these technologies, real-time stock-level information and predictive analytics can be used to optimize ordering quantities and delivery timing. This will reduce minimum safety stocks and overall inventory costs for the customer. Moreover, predictability and service level for the end-consumer can be visibly improved and risks of supply chain disruptions minimized.
If well synchronized with the tools used by consumers, these technologies will be able to support applications such as predictive maintenance. In other words, spare parts can be proactively picked and shipped from the warehouse to the customer before a machine breaks down: just in time for an unscheduled overhaul. Maintenance windows can be narrowed down, and machine efficiency upgraded as a result.
Many production facilities are responding to an incoming fourth industrial revolution, so-called - Industry 4.0. These steps towards Industry 4.0 mean that logistics is also confronted with major changes. The Internet of things will exponentially increase the data volume. If the logistics companies want to keep up with their customers, they will have to adapt their processes and IT to the new demands. The key factors are speed, safety, reliability, increased efficiency and a focus on customer service. For their fulfillment can contribute significantly the use of computer vision.
Computer vision is one of the most advanced areas of computer technology and software development. It is used for object recognition from the captured image that means for processing video or photos. Forward-thinking companies will ensure you gain all the knowledge you need, provide help and plan solutions, to ensure you capitalize on all the latest technologies.
Technology integrally associated with the industry 4.0, which include computer vision, continue to grow very quickly and bring a for logistical and other companies new possibilities. At the end of this voyage is a full automation. Now it is impossible to predict exactly when this will happen, but companies that adapt to this trend in time will undoubtedly have a competitive advantage.
Computer vision brings to the process of identification many advantages such as increased speed, accuracy, or for example feedback thanks to the analysis of captured images. More advanced use of computer vision in autonomous machines such as transport robots in warehouses or drones for the transportation of packages directly to customers without the need for human involvement into the process of their operation, will allow future integration of these devices into the Internet of things and thereby further improve the efficiency in the logistics supply chain.
Lastly, the beauty of today’s mobile technology is that it is ubiquitous: Many people, including the average floor worker in a warehouse, are familiar with the technology. More familiarity means less training needed, fewer errors, and faster pace of work.
So, what do these technology trends mean for the average warehouse or logistics facility? More importantly, where do companies start if they want to exploit these trends? As a first step, warehouse managers need to ask different questions such as does it integrate with our current processes? Will it improve picking times? Will it reduce costs? Is the new technology scalable? Is it faster than what is currently being deployed? And most importantly find a software supplier who can help them answer all these questions.
What will the future warehouse look like in 30 years?
Improved productivity and flexibility while reducing costs, the drudgery of work and environmental footprint will be a given. Automation and robots will continue to replace some of the traditionally labor-intensive roles and monotonous tasks, freeing up time for warehouse staff to complete other fulfilling and more value-adding roles. Interactive and mobile technology, intelligent robots, big data analytics, plug and play automation will have a role to play…
We believe that as new technologies continue to develop, it will significantly change the way goods are received, stored and shipped in a warehouse and will transform the Supply Chain beyond what we currently know.
It’s entirely possible that by the year 2045, the warehouse management system will be much more worthy of the title, able to control every aspect of warehouse operation, including security, receiving, put-away, storage, picking, and dispatch, as well as lighting, temperature control, indirect materials purchasing and even some, if not all, maintenance.
A final thought - will our warehouses over time become fully automated and require no humans?.... Time will tell!
ClarusWMS is a UK based supplier of warehouse management solutions with a wealth of industry experience in third-party logistics, wholesale/retail distribution, online fulfillment and manufacturing warehousing.
Free white paper

WMS software pricing guide
Your up-to-date guide to the cost of WMS software
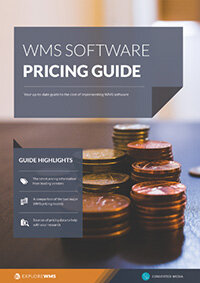
Featured white papers
Related articles
-
Warehouse picking and packing processes: how much labor do you need?
Logiwa's Erhan Musaoglu shows you how to calculate picking and packing labor requirements for you...
-
Mission-critical features of food lot traceability software
What features of food traceability software will help you during a food recall
-
Five key stakeholders in your WMS selection process
The stakeholders you will need on board for your WMS selection project, and what they can offer