Three mistakes small warehouses make when selecting WMS
Speaking with vendors about a robust WMS for your small warehouse can be intimidating. Presentations get flashy and promise gains that are out of this world, but your needs are stuck firmly on the floor. In all the homework and reading you do, things tend to blend together, and it can be difficult to make sure you understand the nuances of offers and tools.
We’ve put together three different kinds of questions and considerations to help you take a moment and think about your WMS on a practical level for today, plus a strategic level for growth beyond tomorrow.
Is the ROI calculation right for you?
One of the hardest tasks for a small warehouse to get right is understanding the ROI calculations you need to use during the selection, implementation, and usage phases. Don’t feel too bad though; it’s also one of the hardest things for large companies to do too.
Start by creating metrics for your existing operations. How long does it take to process an order, fill it, reorder inventory, and have everything you need to keep your warehouse clean and ready to serve your business?
Find the right WMS for your small warehouse with this comprehensive WMS selection checklist
Get your numbers together ahead of time, so you know what you can measure with real data and ask about these elements during your RFP and selection process. Seek a vendor and WMS that directly addresses the areas you want to improve.
A best practice for vendors responding to an RFP is to highlight tangible benefits as well as those more difficult to quantify during the selection process. Look for stats around improve customer service, different types of efficiency gains, employee satisfaction improvements, and more.
Skimping on training questions
Small companies tend just to have a few people who manage their WMS, especially dashboards. This can work out well if you’ve got someone mid-career who plans on staying for quite some time to be your core trainer.
Unfortunately, reality often intervenes, and people change jobs for a variety of reasons. If you don’t train multiple people on each aspect of the WMS, you risk losing institutional knowledge that makes it successful.
When staff aren’t trained on the new WMS or aren’t held accountable, there’s also a chance they won’t use the new system and instead find ways to work around it and stick to old habits. This will harm your ROI as well as the productivity of your warehouse.
So, what does this have to do with selection?
Pick vendors that provide robust training, on-going support, and work with you to establish the right teams to teach. Ask for help and tools to ensure your staff learns the new system correctly and will use it when the time comes.
If training is an afterthought for your vendor, it’ll likely be one for you too.
One day you might not be small
A core benefit of a WMS is its ability to simplify processes while optimizing workflows and reducing manual tasks. There are a variety of automation tools and supports your WMS can have, though you might not turn them all on right away.
Plan for where you project to grow tomorrow, not the minimum specs for today. If you just get what you need to squeak by, you might end up having to buy a whole new WMS and go through all the implementation and training costs again in a year or two.
For example, if you have a WMS that can’t keep inventory levels correct across two warehouses — or it fails to understand multiple locations and makes fulfillment difficult — you can’t use it when you grow larger. It would also limit you from treating two sections of a single warehouse as two locations.
Skimping can often lead to increased costs in the near-term as well as the long-term.
Free white paper

WMS selection checklist
Over 100 actionable steps to WMS selection success
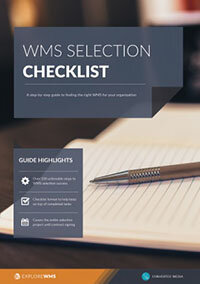
Featured white papers
Related articles
-
How much WMS software costs and how to set your budget
A complete guide to WMS costs, and how to calculate your budget based on these
-
Mission-critical features of food lot traceability software
What features of food traceability software will help you during a food recall
-
Here's your complete WMS modules and features checklist
All the features and modules you might need in your WMS - perfect for requirements gathering