ERP vs WMS: What’s the best software for your business?
What's the best software for your business? That's obvious: the software that makes money. The software that solves problems. The software that makes people’s jobs easier.
Enterprise resources planning software can fit those requirements. So can warehouse management system software. Let's take a closer look at these and perhaps help you shine a light on your own business and whether one of these systems could benefit you.
What is a WMS?
Warehouse management systems are intended to optimize the movement of your inventory. You have items on hand at any time, some on a shelf, some still at the receiving dock, and some at the shipping dock already. You have customer orders in your backlog that might need to be shipped today or they might need to ship at some later time.
In that big mix, what one item should be moved NEXT? And when that one is touched, what is number two? You set the rules that define how the system will work. Is it something a customer needs immediately and he is waiting right now at the door? Is it something that will ship today and happens to be directly in front of one of your warehouse workers for an immediate pick?
Based on the rules you set, WMS will direct your workers to pick, pack, putaway, or maybe just move an item to a better location. Your warehouse will run more efficiently and effectively. You will know where every item is now and where it should be. Your customers will be happy because their orders will be delivered to their expectations.
What is an ERP system?
Enterprise requirements planning systems look at your whole enterprise or business. Typically there are modules for accounting, sales orders, purchase orders, customer requirements planning, production planning and execution, quality control, payroll, human resources, and inventory.
There is some overlap between inventory in ERP and WMS. ERP tracks how many of each item are on hand and how much those items are worth. ERP looks at your customer order backlog and your forecast, compares those demands to current on-hand inventory, and suggests future purchases to bring your supply matched to your demands.
ERP uses database tables shared by all the modules, which ensures consistency across all the functions in your business. Often each module is sold separately so a business only buys those it needs and will use. If your business does no manufacturing, you aren’t required to have production control and routing modules you will never use.
The key difference between WMS and ERP
Warehouse management systems are focused on inventory and the warehouse where that inventory is kept. Enterprise requirements planning systems have a much broader perspective. They are a jack-of-all-trades related to a WMS subject expert. WMS aims for a real-time view of inventory and the warehouse.
WMS is primarily an execution driver. What action needs to happen next? Who will take that action? When that action is complete, what is the next action? ERP takes a more static view of your business. ERP can show how much money is in the bank and how much tomorrow’s payroll will require. It is up to you to actually issue the payments.
ERP might suggest a purchase order is no longer needed and should be canceled or moved to a later date. If no action is taken, ERP will give you the same suggestion tomorrow. ERP has all the data for your entire business and gives you the ability to predict how many engineers you will need next year. ERP can help you know which customers are more profitable and which ones should get less attention from your sales force.
Which system is best for your business?
Both systems have value. Whether they have the value you need for your business is something each business must work out individually. Begin by clearly defining the goals of your business, both long-term and short-term. Understand your current conditions and resources.
What, then, are the gaps between where you are and where you want to be? Which gaps can be filled immediately and which ones are OK to wait to be filled? Work up a list of discrete and measurable requirements. Get consensus across the entire business that your list is complete.
Rank those requirements and draw a line so that all the must-have requirements are above the line and below it are those that might be called “nice-to-have”. Your list will point you toward the system best for your business. If your requirements are moving inventory through your warehouse to your customers, you choose one direction.
If your requirements are accounting-related, such as closing the books earlier in the month, your choice is in a different direction. The answer to which system is better for your business does not have to be either/or. Many businesses will find their requirements spread to both ERP and WMS.
Many ERP systems include a WMS module. This could work for your business. Your WMS will share the same databases as ERP inventory as well as all the other ERP functions. Your WMS will look like and behave for your users just like sales orders and quality control.
Because you all use the same software, everyone in the choir will have the same sheet of music. Be sure all your requirements will be met using this combined system. If you find you have requirements that force different ERP and WMS systems, you can still get custom software to integrate the two.
The additional cost could pay for itself. Today’s software all uses the internet and sharing data across platforms is regularly done. Determine what your business needs to meet your specific requirements. Calculate the initial costs and understand the flow of future costs you will commit to.
Estimate the incremental revenue and cost savings you will achieve through your new software, put those numbers together, and calculate the return on your investment. Does that return meet the threshold returns your business demands? Are you ready to satisfy some of the requirements for your business? Which ERP or WMS software is best for your business?
Free white paper

WMS requirements template
Over 120 WMS feature ideas to help you build a requirements list and shortlist vendors
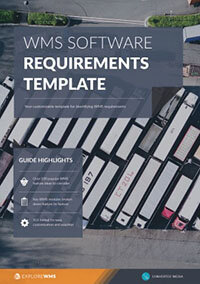
Featured white papers
Related articles
-
How much WMS software costs and how to set your budget
A complete guide to WMS costs, and how to calculate your budget based on these
-
Mission-critical features of food lot traceability software
What features of food traceability software will help you during a food recall
-
Here's your complete WMS modules and features checklist
All the features and modules you might need in your WMS - perfect for requirements gathering